The Reality of Rising Costs in Construction: Why Prefabrication is the Only Path Forward
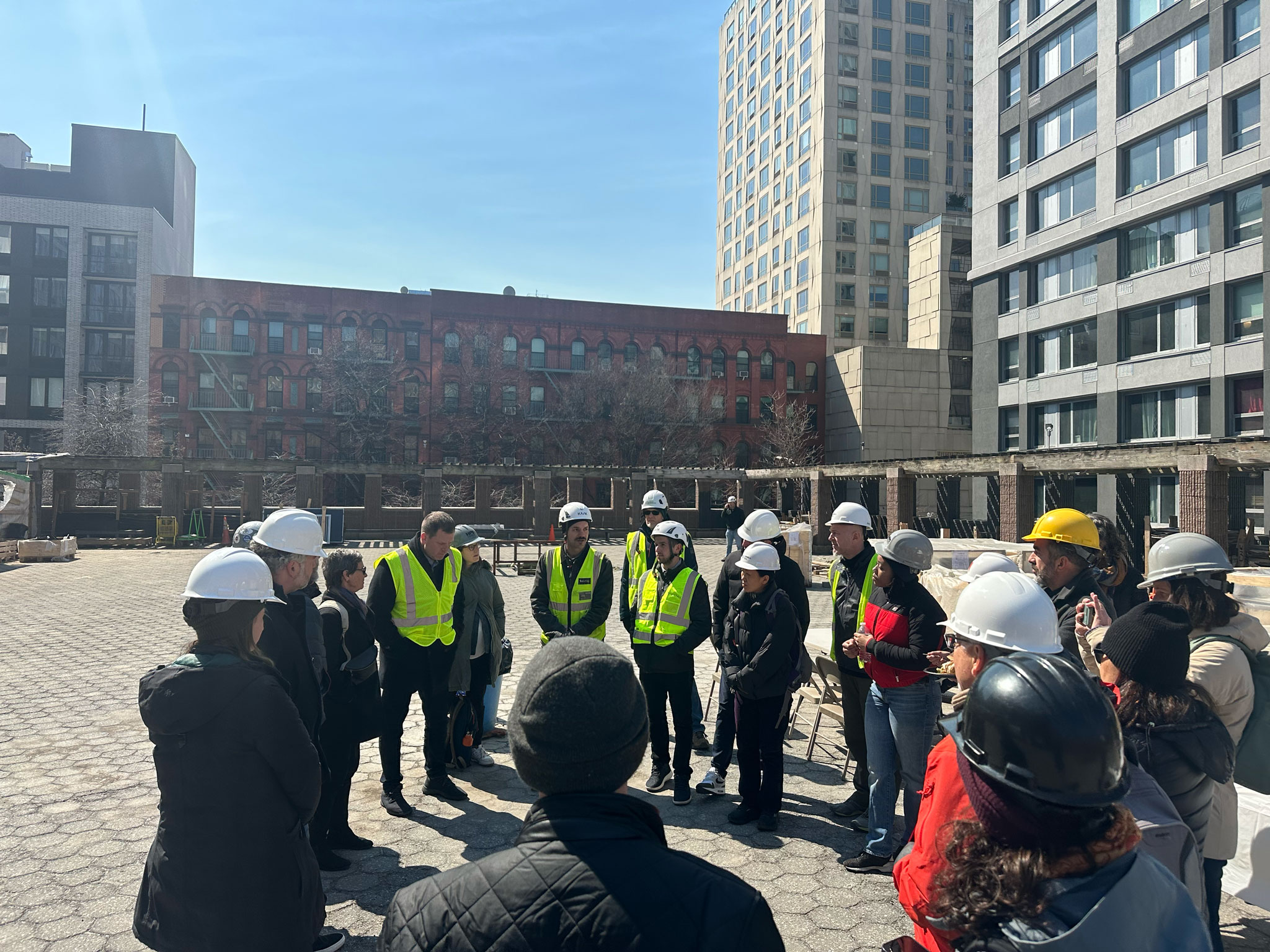
Dear Partners and Colleagues,
Let me say it loud and clear—building material costs are NEVER coming down. That’s right, I said it. And if you’re in the high-rise construction game, you need to stop waiting for a miracle. The industry has changed, and it’s time we face the harsh reality.
We’re all seeing it: material costs are directly tied to global commodity markets, and those are not exactly known for getting cheaper. Steel prices? Up 215% in the last five years. Concrete costs? Also rising steadily. According to Turner & Townsend’s latest report, construction costs jumped 7% in 2023 alone, and they’re forecasted to keep rising.
But that’s not the end of it. Labor costs? They’re not coming down either. We’re in a skilled labor shortage that’s not going anywhere soon. You can’t just pull skilled tradesmen out of thin air, and as a result, labor costs are soaring year after year. The Bureau of Labor Statistics has shown construction wages have increased by 4.5% year-over-year as demand outpaces supply. And if you’re still banking on hiring at a discount—forget it.
So, how do we make projects work? The old tricks won’t cut it. There’s only one way to get numbers to work in today’s climate: reduce construction timelines. And I’m not talking about shaving a few days here and there. I’m talking about drastic reductions. The faster you can get that building up, the faster you can reduce your loan carry costs and start generating revenue. And that’s the only way you’re going to survive in this environment.
How do you reduce timelines? By embracing tech, robotics, and offsite construction practices like prefabrication and modularization. These are the tools that will get you there, and those who don’t adopt them are in for a rude awakening. According to McKinsey, prefabrication can cut project timelines by up to 50%, and modular/prefab construction can result in 20-30% cost savings on average. That’s not theory—that’s real.
At Dextall, we’ve seen this work firsthand. On our 160th Street project in Queens NY, we shaved 3 months off the construction schedule using our prefab exterior wall panels. Three months of loan savings, three months faster to lease-up. That’s real money on the table, not some vague promise. The projects that adopt these innovations are the ones that will succeed.
The days of waiting for cheaper materials and labor are over. The numbers don’t lie, and the market is only getting tighter. The only way forward is faster, more efficient builds through technology and prefabrication.
So, if you’re still stuck thinking that costs will magically drop, it’s time to wake up. The future is already here, and those who embrace it will thrive. The rest? Well, you know what happens.
What’s your plan to reduce timelines and get ahead? Let’s talk.
Sincerely,
Aurimas Sabulis
CEO, Dextall
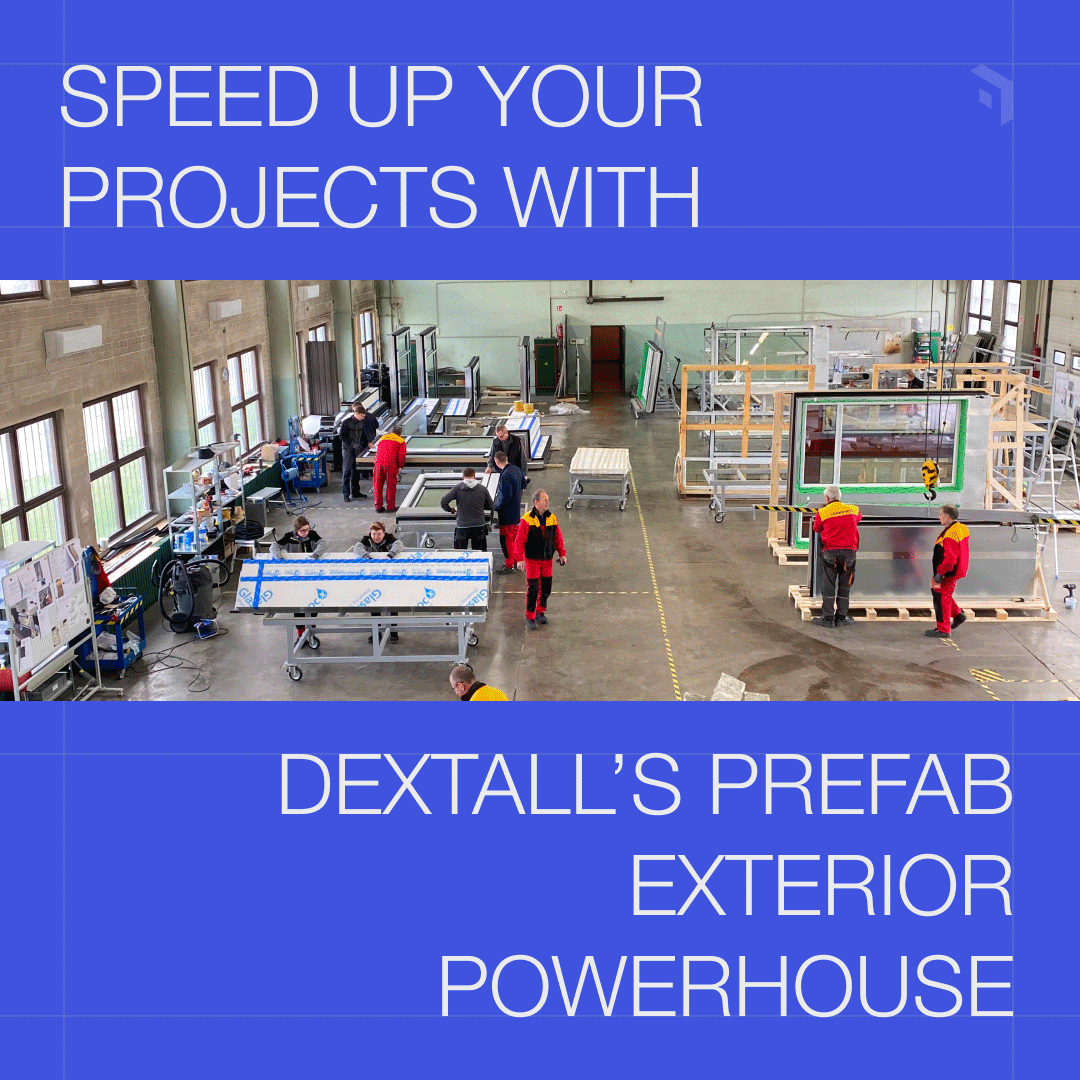